Introduction
A supply-chain manager oversees the movement of goods, from production to distribution. This blog post explores the Life of a Nigerian Supply Chain Manager.
Supply-chain management is crucial in Nigeria for efficient business operations and economic growth.
The day-in-the-life concept provides insight into the daily activities and challenges of a Nigerian supply-chain manager.
Supply-chain management plays a crucial role in the smooth functioning of businesses in Nigeria.
Efficiently managing the flow of goods, from production to distribution, is essential for maintaining customer satisfaction and driving economic growth.
A supply-chain manager’s responsibilities revolve around coordinating and optimizing various processes within the supply chain.
They oversee procurement, production, transportation, warehousing, inventory management, and customer service.
Their goal is to ensure that the right products are delivered to the right place at the right time while minimizing costs and maximizing efficiency.
In Nigeria, where logistics challenges are prevalent, effective supply-chain management becomes even more critical.
The country’s large population and vast geographical expanse pose significant logistical hurdles.
Poor infrastructure, unpredictable socio-political factors, and inadequate technology all contribute to supply chain complexities.
A day in the life of a Nigerian supply-chain manager is filled with challenges and excitement. They start their day by analyzing inventory levels, reviewing production plans, and assessing order fulfillment requirements.
They work closely with suppliers, checking the quality and availability of raw materials.
Throughout the day, they collaborate with different departments, coordinating production schedules, monitoring transportation logistics, and ensuring on-time deliveries.
They constantly communicate with customers, resolving any issues, and providing updates on their orders. They also stay updated on market trends and competition to make informed decisions.
In the end, supply-chain management is indispensable in Nigeria’s business landscape. A well-managed supply chain enhances operational efficiency, reduces costs, and bolsters customer satisfaction.
The day-in-the-life concept allows us to understand the challenges and complexities faced by Nigerian supply-chain managers, highlighting their vital role in the country’s economic development.
Morning Routine
Wake up and preparation for the day ahead
- As a Nigerian supply-chain manager, my day starts early in the morning.
- After waking up, I immediately start preparing myself for the demanding day ahead.
- I freshen up, have a quick breakfast, and make sure to dress professionally.
- Being presentable is essential as I often have meetings with stakeholders and clients.
Review emails and prioritize tasks for the day
- Once I’m all set, I open my laptop and delve into my overflowing inbox.
- Reviewing emails helps me understand any urgent issues that need immediate attention.
- As a supply-chain manager, I deal with various stakeholders, both internal and external.
- Prioritizing tasks based on their urgency and impact is crucial for a smooth workflow.
Conduct team meetings to discuss challenges and set goals
- Next, I gather my team for a morning meeting to touch base about ongoing projects.
- We discuss any challenges and potential roadblocks that may arise during the day.
- Collaborative problem-solving is key to keeping our supply chain efficient and effective.
- During these meetings, we also establish goals and milestones to be achieved during the day.
Read: Best Books for Aspiring Supply-Chain Managers in Nigeria
Managing Suppliers
Contacting local and international suppliers for inventory needs
- As a Nigerian Supply-Chain Manager, one of my primary responsibilities is to reach out to both local and international suppliers.
- I ensure regular communication with these suppliers to meet our inventory needs efficiently and effectively.
- Contacting local suppliers helps us support the local economy and build stronger relationships within our community.
- On the other hand, engaging international suppliers allows us to access a wider range of products and potentially lower costs.
Negotiating contracts and prices with suppliers
- Once we identify potential suppliers, the next step is to negotiate contracts and prices that are mutually beneficial.
- I utilize strong negotiation skills to secure the best possible deals for our company without compromising on quality.
- Negotiating with suppliers involves finding common ground that meets our requirements while allowing them to maintain healthy profit margins.
- This ensures a win-win situation for both parties and helps us establish long-term partnerships with reliable suppliers.
Assessing supplier performance and ensuring quality control
- Managing suppliers also involves assessing their performance regularly to ensure consistency and reliability.
- Through regular performance evaluations, we can identify any areas of improvement and address them promptly.
- Quality control is another crucial aspect of managing suppliers to maintain the highest standards in our products.
- I establish quality control measures and work closely with suppliers to ensure they comply with our requirements and deliver superior products.
In fact, as a Nigerian Supply-Chain Manager, managing suppliers is a vital part of my role.
Contacting both local and international suppliers, negotiating contracts and prices, and assessing supplier performance are all tasks that require careful attention.
By maintaining strong relationships with suppliers and ensuring quality control, we can meet our inventory needs efficiently and consistently deliver high-quality products to our customers.
Read: Nigeria’s Supply-Chain: A Regional Comparison
Monitoring Inventory
As a Nigerian Supply-Chain Manager, monitoring inventory is a crucial aspect of my daily routine.
This responsibility encompasses managing stock levels, analyzing trends, forecasting demand, and implementing inventory management systems to optimize efficiency and profitability.
Managing stock levels and ensuring availability of essential items
One of my primary tasks is to manage stock levels in our supply chain. I constantly monitor inventory to ensure we have an adequate quantity of essential items.
This involves tracking the movement of goods, assessing stock levels, and forecasting future needs.
By maintaining optimal stock levels, I can ensure that our company has sufficient inventory to meet customer demands and minimize the possibility of stockouts or overstocking, which can result in financial losses and dissatisfied customers.
Analyzing trends and forecasting demand
To effectively manage inventory, I analyze trends and forecast demand. This involves meticulously examining historical sales data, market trends, and customer preferences.
By understanding these indicators, I can make informed decisions about inventory volumes and procurement strategies.
Accurate demand forecasting enables us to adjust stock levels accordingly, ensuring that we have enough inventory to fulfill customer orders without excessive storage costs or tying up capital in unnecessary stock.
Implementing inventory management systems
To streamline and optimize inventory management, I implement robust systems and processes.
This includes using technology-driven solutions to track inventory levels accurately, automate reordering, and minimize manual errors.
By implementing inventory management systems, we can improve efficiency, reduce costs, and enhance overall supply chain performance.
These systems also provide real-time data and analytics, enabling us to monitor stock levels, identify potential issues, and make data-driven decisions.
Moreover, utilizing modern technologies such as radio frequency identification (RFID) or barcode systems enhances the accuracy and speed of inventory monitoring, eliminating human errors and increasing productivity.
In general, monitoring inventory as a Nigerian Supply-Chain Manager is an essential responsibility.
It involves managing stock levels, ensuring availability of essential items, analyzing trends, forecasting demand, and implementing inventory management systems.
By effectively monitoring inventory, we can optimize efficiency, mitigate risks, and maintain customer satisfaction in our supply chain operations.
Read: Supply-Chain Management Certifications in Nigeria
Coordinating Logistics
Collaborating with transportation providers for timely product delivery
- A Nigerian supply-chain manager plays a crucial role in organizing the logistical operations.
- Collaborating with transportation providers is essential to ensure timely delivery of products.
- It involves negotiating contracts, rates, and schedules with various local and international carriers.
- The supply-chain manager must stay updated on transportation trends and industry regulations.
Tracking shipments and ensuring compliance with regulations
- Tracking shipments throughout the process is crucial to ensure their smooth movement.
- They need to coordinate with carriers and keep customers informed about the status of their orders.
- Ensuring compliance with regulations and customs requirements is of utmost importance.
- The supply-chain manager must be well-versed in customs documentation and clearance processes.
- Overseeing paperwork for imports and exports ensures seamless movement across borders.
Solving logistical challenges and optimizing routes
- Solving logistical challenges requires a proactive approach and problem-solving skills.
- Unexpected events, such as delays or disruptions, need to be addressed promptly.
- Optimizing routes and modes of transportation helps in reducing costs and improving efficiency.
- The supply-chain manager analyzes data to identify opportunities for streamlining operations.
- They collaborate with internal teams and external partners to implement these improvements.
- Utilizing technology and software tools can assist in optimizing logistics operations.
- Automated systems aid in tracking shipments, managing inventory, and forecasting demand.
- The supply-chain manager must stay updated on the latest advancements in logistics technology.
- Regularly evaluating the performance of transportation providers is essential for ongoing improvements.
- They assess factors like delivery times, reliability, costs, and customer satisfaction.
- Based on the evaluations, decisions are made regarding the continuation or termination of partnerships.
Read: Top Companies Hiring Supply-Chain Managers in Nigeria
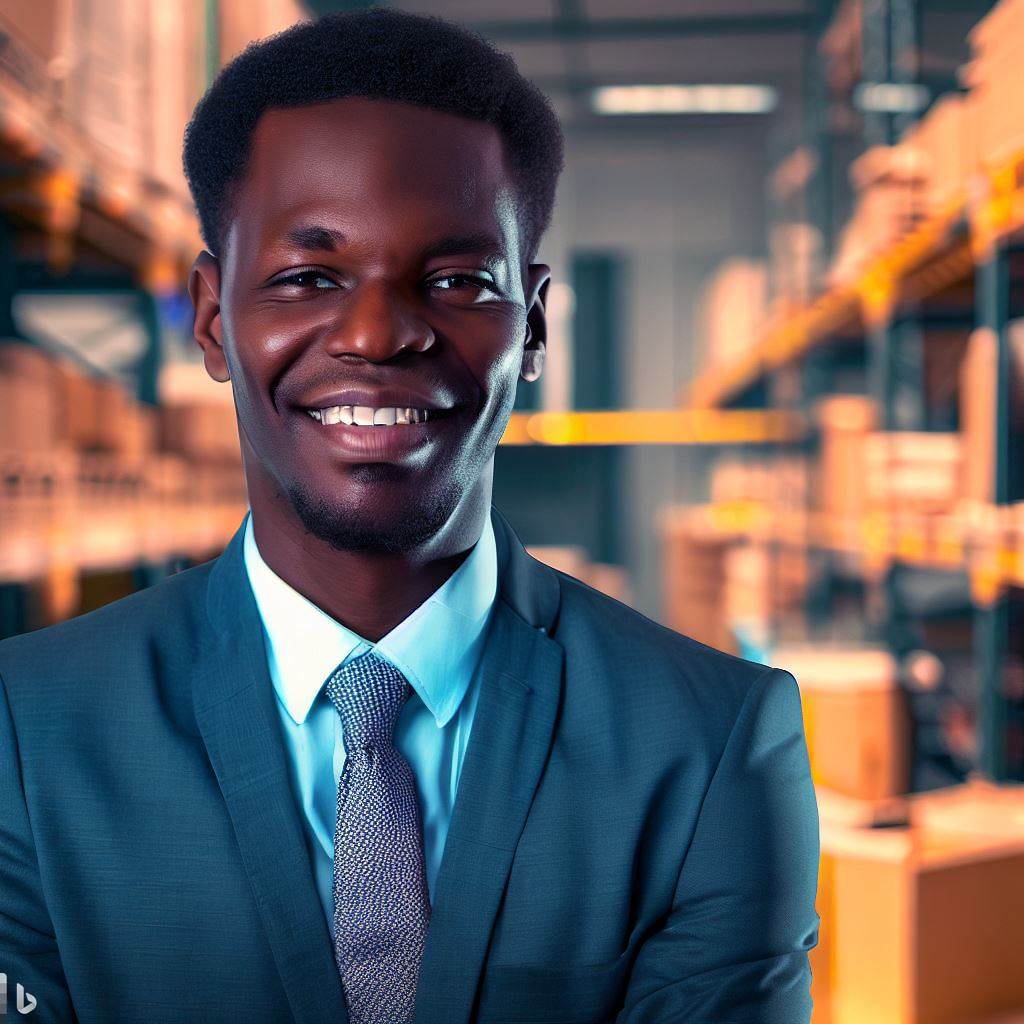
Overcoming Challenges
Dealing with supply-chain disruptions, such as delays or product scarcity
As a Nigerian supply-chain manager, I often face the daunting task of handling various disruptions that can affect the flow of goods and resources. One of the most common challenges is dealing with delays in the supply chain.
Delays can occur due to a multitude of reasons, including transportation issues, customs hold-ups, or even natural disasters.
These disruptions can have a significant impact on the overall efficiency of the supply chain and can lead to product scarcity.
To overcome these challenges, I rely on proactive planning and effective communication. By having contingency plans in place, I can minimize the impact of delays and ensure a smooth flow of goods.
This involves working closely with suppliers, transporters, and other stakeholders to identify potential bottlenecks and find alternative solutions.
For instance, if there is a delay in the delivery of raw materials, I would immediately reach out to the supplier to understand the cause and potential resolution.
By staying in constant communication, I can adjust production schedules and coordinate with other departments to mitigate any shortage that may arise.
Furthermore, I actively monitor market trends and economic indicators to anticipate potential disruptions.
By staying informed about changing trade policies, currency fluctuations, and political developments, I can quickly adapt my strategies to mitigate risks and maintain a stable supply chain.
Handling customs and trade complexities in Nigeria
Dealing with customs and trade complexities is a daily reality for supply-chain managers in Nigeria. The country’s complex import regulations and bureaucratic procedures can pose significant challenges.
To navigate these complexities, I ensure that I have a deep understanding of the customs requirements and regulations.
This includes staying updated with changes in import and export policies, trade agreements, and tariff schedules.
I work closely with customs brokers and legal experts to ensure compliance with all necessary documentation and procedures.
This involves meticulously preparing import and export documentation, including invoices, packing lists, and certificates of origin.
Additionally, I maintain a strong relationship with customs officials and regulatory authorities by attending industry conferences and actively participating in trade-related events.
This helps me stay informed about any upcoming changes in trade regulations and allows me to build rapport with key personnel.
Developing contingency plans to mitigate risks
In order to mitigate risks associated with supply-chain management in Nigeria, it is crucial to have well-developed contingency plans.
I regularly assess potential risks and develop strategies to address them. This includes identifying alternative suppliers or transportation routes to mitigate the impact of disruptions.
By diversifying our supply base and establishing relationships with multiple suppliers, we can minimize the risk of product scarcity.
I also invest in technology and data analytics to enhance supply-chain visibility and improve forecasting accuracy.
By leveraging real-time data and predictive analytics, I can proactively identify potential bottlenecks and take preventive measures to ensure uninterrupted flow.
Moreover, I believe in continuous improvement and regularly evaluate our supply-chain processes to identify areas for optimization.
This includes streamlining procedures, reducing lead times, and enhancing communication and collaboration among various stakeholders.
Overall, overcoming challenges in supply-chain management requires a combination of proactive planning, effective communication, and adaptability.
By anticipating risks, staying informed, and developing robust contingency plans, I can successfully navigate the complexities of the Nigerian supply chain and ensure the smooth flow of goods and resources.
Gain More Insights: Salary Expectations for Project Managers in Nigeria in 2023
Collaboration with Other Departments
Communicating with production, sales, and finance teams
- In my role as a Nigerian supply-chain manager, one of my key responsibilities is to ensure effective communication with various departments within the company.
This includes the production, sales, and finance teams. - I regularly interact with the production team to understand their requirements and relay them to the suppliers.
- By communicating their needs and expectations, I can ensure a seamless flow of materials from the suppliers to the production floor.
- This collaboration helps in aligning production schedules with the availability of raw materials and components.
- Similarly, I work closely with the sales team to gain insights into customer demand and market trends.
- By staying informed about upcoming promotions, new product launches, and changes in customer preferences, I can effectively plan and manage inventory levels.
- This collaboration allows us to fulfill customer orders efficiently and avoid stockouts or excess inventory.
- Additionally, I collaborate with the finance team to ensure that our supply-chain activities are aligned with the company’s financial objectives.
- By providing them with accurate forecasts and cost analysis, they can make informed decisions regarding budget allocation and cost control.
- This collaboration helps in optimizing our supply-chain processes and minimizing unnecessary expenses.
Coordinating efforts to meet company objectives
- As a Nigerian supply-chain manager, I play a crucial role in coordinating efforts across different departments to achieve our company’s objectives.
- By understanding the goals and targets set by top management, I can align the activities of production, sales, and finance teams accordingly.
- For example, if the company’s objective is to increase market share, I will collaborate with the sales team to ensure sufficient product availability and timely delivery to customers.
- I will also work with the production team to streamline operations and eliminate bottlenecks that may hinder timely order fulfillment.
- Similarly, if the company aims to reduce costs, I will collaborate with the finance team to identify areas of cost-saving potential within the supply chain.
- By analyzing transportation routes, sourcing strategies, and inventory management practices, we can develop efficient and cost-effective solutions.
- Overall, by coordinating efforts and aligning departmental activities, we can work towards achieving our company’s objectives more effectively and efficiently.
Ensuring alignment between departments for efficient operations
- Efficient operations require alignment between various departments, and as a Nigerian supply-chain manager, it is my responsibility to ensure this alignment.
- I regularly schedule cross-departmental meetings to foster collaboration and discuss any challenges or opportunities that may arise.
- These meetings provide a platform for open communication and help identify areas where cooperation is needed for improved efficiency.
- By encouraging open dialogue and fostering a spirit of teamwork, I ensure that everyone understands the impact their actions have on the overall supply chain.
- This alignment is crucial to avoid any conflicting objectives or actions that might disrupt the smooth flow of materials and information.
- Furthermore, I promote a culture of continuous improvement, where employees from different departments actively contribute their ideas and insights for optimizing operations.
- This collaborative approach leads to innovative solutions and ensures that the supply chain remains agile and responsive to changing market dynamics.
In essence, effective collaboration with other departments, such as production, sales, and finance, is crucial for a Nigerian supply-chain manager to achieve efficient operations and meet company objectives.
By communicating effectively, coordinating efforts, and ensuring alignment, we can streamline our supply-chain processes and drive overall success.
Continuous Improvement and Professional Development
Staying updated with industry trends and best practices
In the fast-paced and ever-evolving world of supply chain management, staying updated with industry trends and best practices is crucial for success.
As a Nigerian supply-chain manager, I prioritize continuous learning and seek opportunities to enhance my knowledge and skills.
I regularly read industry publications, participate in webinars, and follow influential professionals on social media platforms to stay informed about the latest trends and innovations.
This enables me to adapt to the changing landscape and make informed decisions that positively impact our supply-chain operations.
By keeping myself updated, I can identify emerging technologies, such as blockchain or artificial intelligence, that have the potential to revolutionize supply chain practices.
Understanding these advancements allows me to evaluate their relevance to our operations and explore potential implementation strategies.
Attending conferences and networking with other supply-chain professionals
Attending conferences and networking events is another important aspect of my professional development.
These events provide opportunities to connect with other supply-chain professionals, share experiences, and learn from their successes and challenges.
By engaging in meaningful conversations and building relationships, I can expand my professional network, which often leads to valuable collaborations and partnerships.
These connections provide a platform for exchanging ideas, seeking advice, and staying updated on industry developments.
Additionally, conferences offer sessions and workshops conducted by industry experts.
Participating in these educational forums allows me to gain insights into best practices and learn about innovative strategies adopted by leading companies.
By applying these learnings to my own work, I contribute to the continuous improvement of our supply-chain operations.
Implementing process improvements within the supply chain
As a supply-chain manager, I am responsible for ensuring efficient and effective processes within our supply chain.
Continuous improvement is at the core of my role, as it enables us to enhance productivity, reduce costs, and deliver better customer experiences.
I collaborate with cross-functional teams to identify areas for improvement and implement necessary changes.
This involves analyzing data, conducting root cause analyses, and designing and implementing process enhancements.
By embracing lean principles, we eliminate waste and streamline operations, leading to cost savings and improved overall performance.
We also leverage technology to automate manual tasks, enhance visibility, and optimize inventory management.
Publish Your Professional Profile, Business or Brand
Showcase your expertise, gain trust, and boost visibility instantly on Professions.ng.
Publish NowRegular performance reviews and audits allow us to identify bottlenecks, address inefficiencies, and develop action plans for continuous improvement.
By involving the entire supply-chain team in these efforts, we foster a culture of innovation and collectively strive for excellence.
In a nutshell, continuous improvement and professional development are integral to the role of a Nigerian supply-chain manager.
Staying updated with industry trends, attending conferences, and implementing process improvements contribute to our success in a dynamic and competitive environment.
Conclusion
A day in the life of a Nigerian supply-chain manager is filled with diverse responsibilities. From coordinating logistics to managing inventory, they play a crucial role in ensuring the smooth operation of businesses.
Supply-chain managers in Nigeria are responsible for overseeing the entire process of delivering goods and services to customers.
They must collaborate with different teams, from procurement to transportation, to maintain an efficient supply chain.
Additionally, these professionals have the task of forecasting demand and planning for future needs.
By analyzing data and market trends, they can optimize inventory levels and minimize costs, ensuring profitability for the business.
The role of a Nigerian supply-chain manager is vital for business success.
Their ability to streamline operations and meet customer demands directly impacts the company’s reputation and financial performance.
Moreover, supply-chain management offers an exciting career path for future professionals.
It combines problem-solving, strategic planning, and collaboration, making it suitable for individuals with a passion for logistics and efficiency.
By considering a career in supply-chain management, aspiring professionals can be part of driving operational excellence, enhancing customer satisfaction, and contributing to the growth of Nigerian businesses.
Nigerian supply-chain managers hold a significant role in ensuring the success and growth of businesses through effective management, innovation, and strategic decision-making.